SELLADO HORIZONTAL
La barrera horizontal (inyección a presión) es un sistema de sellado contra la humedad por capilaridad. Hoy en día se tiende cada vez más a aprovechar los sótanos como espacios habitables. Para satisfacer esta exigencia de calidad, en muchos casos, se realiza, en las paredes húmedas, una impermeabilización posterior de la obra por parte de un profesional. En el caso de cavidades, estas son rellenadas previamente con pasta de cemento. El objetivo de la barrera horizontal es constreñir los vasos capilares en el material de construcción, para evitar que siga aumentando la humedad y para reducir el contenido de humedad en la mampostería. El relleno del hueco y la inserción de una barrera horizontal a través del mismo se realizan mediante el mismo sistema packer.
Ventajas y Beneficios
- Consolidación y estabilización de paredes en la zona de la inyección.
- Bajo consumo de fluido de inyección mediante el relleno previo de la cavidad.
- Menos accesorios necesarios para, por ejemplo, un menor desgaste del taladro y una menor utilización de packers.
- Reducción del tiempo de trabajo por metro.
Ejemplos de aplicación
- Puede aplicarse posteriormente en construcciones antiguas.
- En función del grado de humedecimiento del objeto, se utilizan diferentes métodos para su aplicación.
- Un examen previo es imprescindible para determinar la aplicación de las medidas correctivas.
- Las barreras horizontales deben efectuarse en toda la sección transversal del componente.
Campos de aplicación
- Pared de mampostería con huecos.
- Pared de ladrillo homogénea.
- Pared de ladrillo homogénea con baja alcalinidad y un grado de humedecimiento > 80 %
MÁS SOBRE LOS DIFERENTES PROCEDIMIENTOS
MÁS SOBRE LOS DIFERENTES PROCEDIMIENTOS
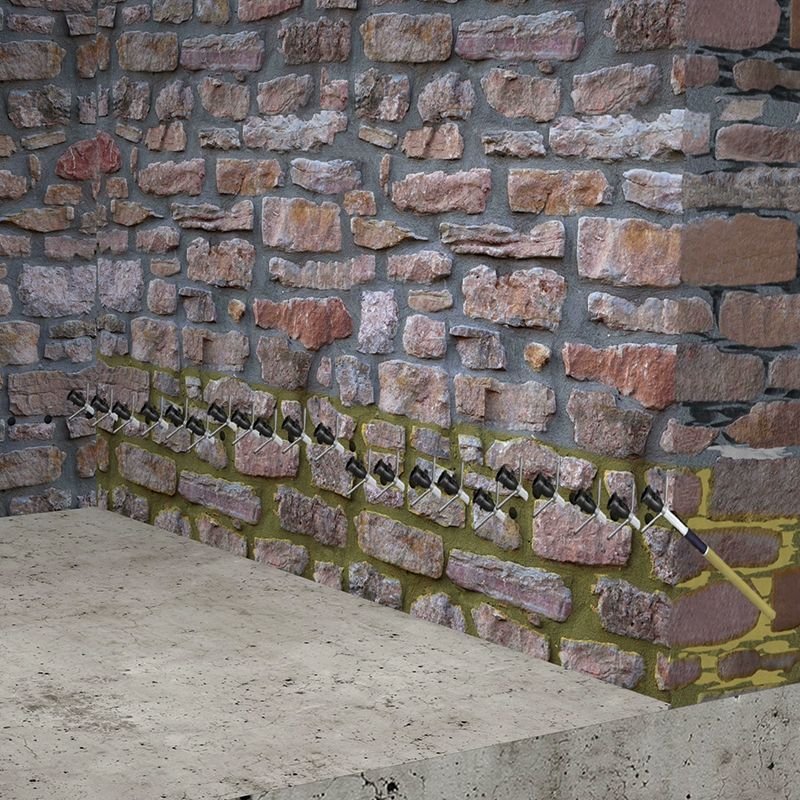
MÉTODO DE INYECCIÓN PARA MAMPOSTERÍA CON CAVIDADES
Mediante una inyección multietapa en un proceso de baja presión, y gracias a los packers de perforación, las cavidades, defectos y fisuras se rellenan con un mortero de inyección sin contracción. Usando los mismos packers, se crea un canal de perforación con una lanza. El material de inyección se inyecta a continuación mediante una inyección a presión (3 – 5 bares) para una mejor distribución. De esta manera se puede lograr una eficacia óptima en el campo de la mampostería inyectada.
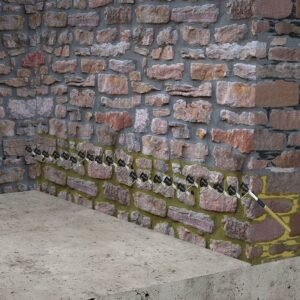
MÉTODO DE INYECCIÓN PARA MAMPOSTERÍA CON CAVIDADES
Mediante una inyección multietapa en un proceso de baja presión, y gracias a los packers de perforación, las cavidades, defectos y fisuras se rellenan con un mortero de inyección sin contracción. Usando los mismos packers, se crea un canal de perforación con una lanza. El material de inyección se inyecta a continuación mediante una inyección a presión (3 – 5 bares) para una mejor distribución. De esta manera se puede lograr una eficacia óptima en el campo de la mampostería inyectada.
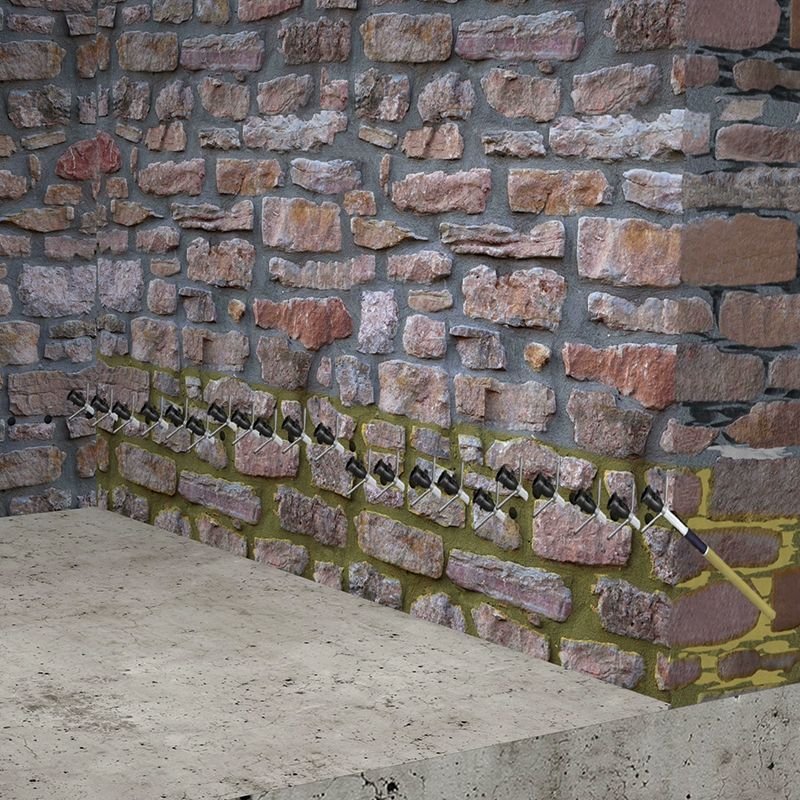
MÉTODO DE INYECCIÓN PARA MAMPOSTERÍA CON CAVIDADES
Mediante una inyección multietapa en un proceso de baja presión, y gracias a los packers de perforación, las cavidades, defectos y fisuras se rellenan con un mortero de inyección sin contracción. Usando los mismos packers, se crea un canal de perforación con una lanza. El material de inyección se inyecta a continuación mediante una inyección a presión (3 – 5 bares) para una mejor distribución. De esta manera se puede lograr una eficacia óptima en el campo de la mampostería inyectada.
MÉTODO DE INYECCIÓN PARA MAMPOSTERÍA HOMOGÉNEA
El material de inyección seleccionado se inyecta en el componente mediante una presión continua (3 – 5 bares), que se ajusta al componente, a través de packers de perforación. Es importante asegurar una distribución relativamente uniforme del material de inyección a fin de garantizar la formación adecuada de una zona efectiva. Por consiguiente, según las condiciones del componente, la presión de inyección debe mantenerse durante un período más largo (por ejemplo, varios minutos por packer).
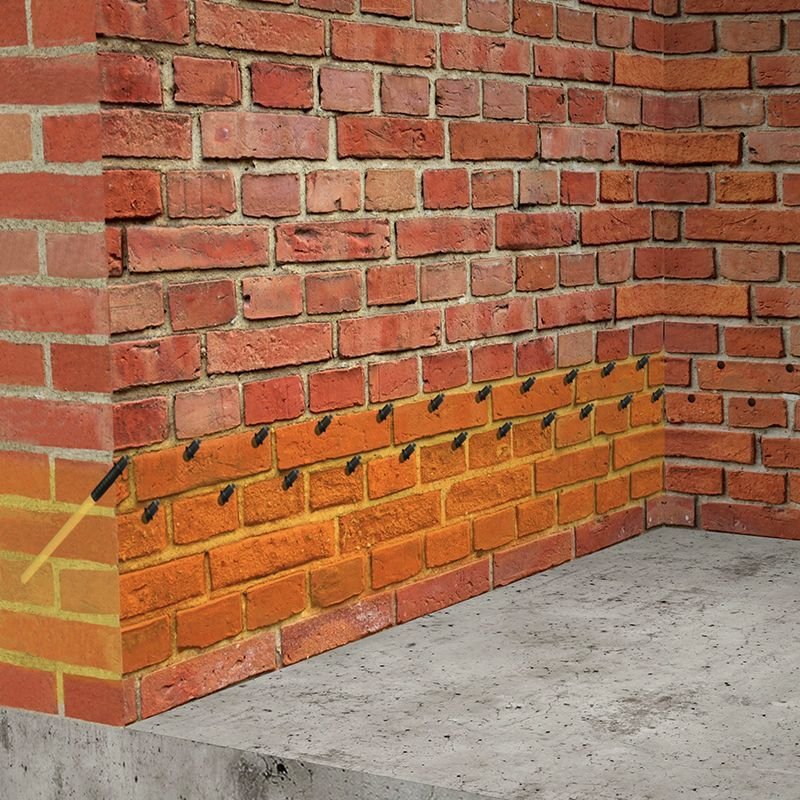
MÉTODO DE INYECCIÓN PARA MAMPOSTERÍA HOMOGÉNEA
El material de inyección seleccionado se inyecta en el componente mediante una presión continua (3 – 5 bares), que se ajusta al componente, a través de packers de perforación. Es importante asegurar una distribución relativamente uniforme del material de inyección a fin de garantizar la formación adecuada de una zona efectiva. Por consiguiente, según las condiciones del componente, la presión de inyección debe mantenerse durante un período más largo (por ejemplo, varios minutos por packer).
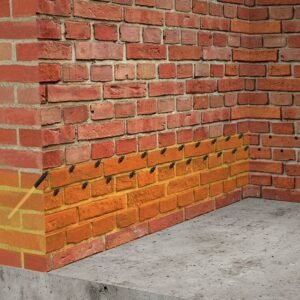